__________________________________________________________________________
This is the third installation of my window seat and book case project. In Part I, I showed how Mr. Vagabond and I plotted the layout and started building the framework. Part II shows real progress with the bones of the window seat and book case really taking shape. In this installation, Part III, we’ll take a look at some finishing work issues that arose and how we worked around them.
Throughout this project, I learned one very annoying thing: It’s not easy to find a straight board. At the finishing carpentry stage, I also discovered that it’s not necessarily a good idea to buy small boards in strapped bundles.
We needed 1 x 2 pine boards to use as cleats, which would support the shelves. We bought a bundle of “premium” boards that looked pretty straight. The label gave me some confidence about the purchase:
See? Premium lumber. It has to be good, right? We were disappointed when we cut the straps on the bundle at home.
Aside from the fact that there was not a single straight board in the bundle, we also discovered this:
This made me wonder what other grades they carry besides “premium” and what those grades look like. The challenges that this premium lumber presented were wrestling with each of the boards to mount them relatively straight, and sanding off the rough, gnawed-looking texture. Thankfully, 1 x 2s are thin and light, so we were able to force them into position as we screwed them into place. To do that, we marked off the level line where the board would mount, pre-drilled the holes and then fastened a board with one screw. After one screw was inserted we pushed or pulled to align the board, and then fought with the rest until it was secure and somewhat straight. Never underestimate the importance of checking the lumber that you buy to ensure that it’s straight. If there are several boards strapped into a bundle, cut the bundle and check each one.
Sanding off the coarse surface proved to be an impossible feat. The more I sanded, the worse it looked. It went from jagged to fuzzy, and never improved from that point. I turned the most awful side toward the wall, and let the least awful side face out. Because I needed nice-looking boards for the front edge of each of the shelves, we made another trip and bought cedar 1 x 2s. They had beautiful, clean, straight edges.
Most of the materials that we used were pine. Additionally, we used poplar plywood and some cedar trim. Staining the three to look reasonably uniform was challenging, but it worked out.
There’s a trick to nailing a board and then hiding those nails, and that trick is called “countersinking.” Finish carpenters know this trick well, and it is one way to make your project look more professional. This is a close-up image of one of the cedar boards after I had driven in a finishing nail. Notice that the small nail head stands proud of the face of the board. Also note the small depression in the center of the nail head.
![]() |
The plywood peeking out under the cedar board would eventually be covered with fancy trim molding. |
I drove in each nail, leaving the head proud of the boards by about 1/16 inch. This saved the boards from being dented by the hammer. Countersinking the nails requires a small tool called a nail set, or you can also use a larger nail or a screw, like I am using here. Anything with a small tip and a head that you can whack with a hammer will sink the nails.
Tap the nail set or nail or screw with a hammer, driving in the nail until it looks like the next photo. This leaves a small depression that you can fill with stainable wood putty, or caulk if you plan to paint the board.
After the book cases were finished, we started on the cabinet doors. The left and right cabinets needed doors, and we worked around the nailed-down bench seat by building doors for the front side of the window seat. In this photo, the doors are only set into place and held there with shims. This just gave us an idea of how it would look once the doors were hung.
The doors were another very simple design. I cut 1 x 4s with 45-degree mitered corners, forming a frame that fit each opening. Then I covered the back side with plywood. It’s wise to measure each opening separately and build each door to fit those measurements. Measuring one opening and building the doors the same will invariably result in one door that doesn’t fit. After cutting the frame boards, I set them on a very sturdy and very flat surface, pre-drilled through the corners of the frame and nailed the assemblies together. You can use wood glue for a tighter fit at the joints, if you like, but it wasn’t necessary with ours. This is basic joinery; a butt joint. Butt joints are where two pieces of wood are butted together and fastened. If you have mad woodworking skills, you’ll probably want a fancier, sturdier joint.
Covering the back side of the door frames was fairly easy. I cut the plywood approximately 1 inch smaller on each side, making a piece that fit the opening, and with a generous amount of excess past the edges of the frame opening on the back side. After laying the plywood on the back side of the frame and nailing it down, I secured each edge of the plywood to the frame with very plain, narrow, lipped molding. The small lip slips over the edge of the plywood and fits flush for a clean, tidy look on the back side of the doors.
At this stage of the game, we were really starting to see major improvement. The whole room took on a more finished look, which is saying a lot. The living room has been one of the biggest challenges in the renovation. It’s a little over 12 feet wide, but almost 30 feet long. The window seat and book cases helped balance the room tremendously, making it feel less like a shotgun and more like a living space.
My next and last installment will be staining the book case, and a special treatment that I am still applying to the back wall inside each of the book shelves.
XOXO
XOXO
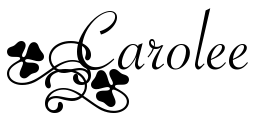
Loving this series. Can't wait to see the staining process! :)
ReplyDeleteThank you! It was a whole lot of fun to build. :-)
ReplyDeleteA thumbs up this construction works, looking forward to see the outcome. I had an almost similar wood working in my bed room, but this one is a cabinet for keeping clothes and personal belongings. In this kind of project we are able to use and hone our carpentry skills for DIY and for livelihood means. By the way, have a great day.
ReplyDelete